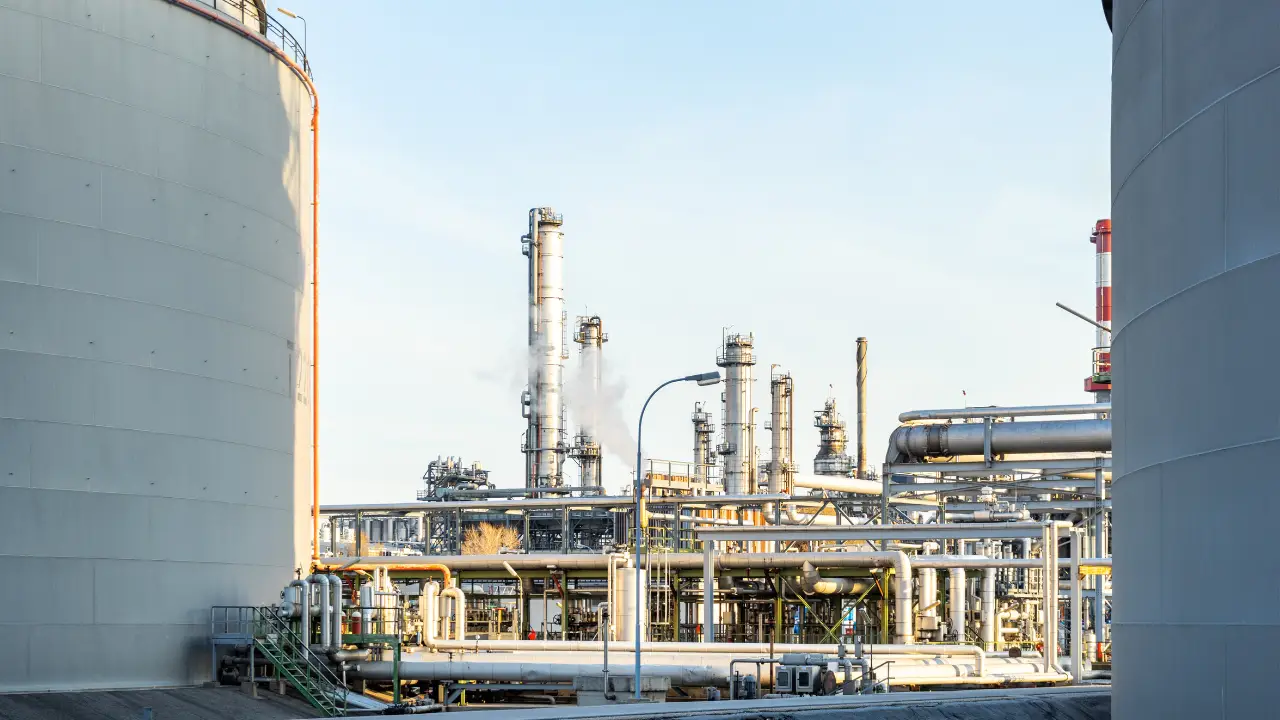
Why Behavior Based Safety Programs Fall Short
Over the years, our collaboration with hundreds of global clients has enriched our expertise in Behavioral Based Safety (BBS) observation programs. These programs blend 1950s’ observation techniques from the Ohio Safety Council with groundbreaking behavioral psychology, thanks to B.F. Skinner. Their goal? To spot and curb “at-risk” behaviors, steering employees towards safer working habits.
This approach has revolutionized safety practices worldwide. The rise in BBS programs and consultants has spurred lively discussions on everything from behavior specifics to effective ways of showing appreciation. Yet, the core idea remains invaluable: watching how work is done, then planning and acting to reduce risks. These programs often see an immediate drop in incidents, a change too significant to attribute solely to the Hawthorne Effect. Despite their benefits, some users have noted a lesser return on their substantial investments.
When BBS first appeared in the early 1980s, it was celebrated as a groundbreaking method for preventing injuries. It appeared beneficial for all – management received an employee-driven safety scheme, safety professionals retained their roles without the need for deep psychological expertise, and hourly workers gained a sense of control, ownership, and even perks like all-expenses-paid conference trips. Consequently, many companies quickly adopted it.
Initially, most adopters saw a decrease in incidents, usually lasting 2-4 years. But then, some reported a stagnation or, alarmingly, a return to previous or higher injury rates. Our analysis of these programs pinpointed four key reasons for their limited success or outright failure. The good news? We have tried-and-true solutions that can help BBS programs achieve their full potential.
We’ll explore 4 reasons “Why BBS Programs Fall Short” and our solutions.
1. The Magic Elixir
Sometimes purveyors of BBS imply that it is a panacea and that simply by implementing their program all of their customer’s safety issues will disappear. Behavioral observations are only a small part of any well founded EHS Management System. There are dozens of other prevention activities which address different skills sets and different situations. Behavioral observations alone can’t replace task analysis, shift starter meeting, “What-If” Drills, etc. nor fix issues with Management of Change, Mechanical Integrity or Operator Training. Too often we have seen companies purchase and implement BBS at the expense of other more glaring deficiencies in their safety programming. In these instances it is not that behavioral observations shouldn’t be used in improvement efforts, it is just that observations can’t be the only tool for improvement.
SOLUTION
If you believe the issues keeping you from achieving the culture and performance you desire are more than those addressed by a traditional BBS program, then consider a comprehensive solution like SRI’s Structured Safety Process™ (SSP). SSP combines viable aspects of your current programming with necessary structure, systems and activities producing a process which far out perform BBS programs. SSP integrates safety into all aspects of your business, incorporating a common approach, which eliminates the gaps between organizations and functional groups. SSP also emphasizes “how” an organization is going to accomplish its goals, as well “who” does “what”, “when” and “why.” SSP brings structure to a wide range of safety activities and effectively integrates them into a functional whole that delivers value in excess of the sum of its parts.
2. Inadequate participation
Most HSE Policy Statements articulate that safety is a core value and it is the responsibility of all employees. BBS Programs are primarily voluntary in nature. Employees volunteer to be trained observers. After training they typically conduct their observations when, where, and observe whom they deem appropriate. Employees grant permission to be observed. Employees that are in the greatest need of observation and feedback decline to be observed at a disproportionately high level. Some observers suffer “burn out” and either cease observing or greatly reduce the number and/or quality of observations. Most BBS Programs are employee centric with Management and Supervision primarily responsible for providing resources and granting employee’s permission to conduct an observation upon request. They have little to no role in conducting observations themselves. Finally, there is a whole subset of employees who choose not to participate at all. To address these deficiencies management often tries to incentivize (pay to play) participation. We have analyzed dozens of observation programs over the years where compensation was awarded for number of observations, successfully completing observation training, being observed, etc. As part of this effort we interviewed thousands of employees gathering their perceptions about the incentive program’s effectiveness. They consistently testified that they participated only to the degree necessary to achieve the reward. Their focus was primarily on quantity and not improving safety.
SOLUTION
A. SRI believes all personnel must be engaged in observing and eliminating safety errors. Our employee based observation process is Accident Projection Techniques™ (APTs), an American Chemistry Council best practice. APTs require all employees to continuously test and challenge the work environment and positively intervene when they come upon a potentially hazardous situation. This can be an at-risk behavior and/or unsafe condition. APT data is used for trend analysis and improvement planning also.
B. The Line Organization (Managers and Supervision) should also participate in the observation process by completing Task Safety Observations (TSOs). TSOs verify work is being conducted safely and correctly while also validating the accuracy of the work instructions (Procedures and Job Safety Analysis). Participation by employees in these is not discretionary.
C. The practice of paying employees extra to participate in the BBS program blurs the fundamental concept that safety is an equal an integral part of every job, task and decision. It is part of core work. Employees should be recognized, encouraged but not compensated for being trained observers.
3. Not all errors addressed
Most BBS programs analyzed were primarily sold as a means to reduce at-risk behaviors and either didn’t, or only minimally, included errors related to substandard conditions. Programs which included conditions typically only expected the employee to identify hazards and not mitigate the errors they have discovered. Each of these situations generates some level of discomfort. Programs which didn’t sufficiently include conditions lead employees to testify that “the company is willing to blame us, but not willing to put their money where their mouth is.” When the only requirement was to check a box valuable opportunities to create ownership, foster stewardship and immediately remove errors from the workplace are lost.
SOLUTION
A comprehensive observation process should address behaviors, conditions, work instructions (SOPs, JSAs) and training. By including conditions you provide a platform for employees to remediate those they can fix and report those which require attention by others. Combining this with feedback regarding pertinent safety related work orders allows management to demonstrate its commitment to employee safety.
4. Observation data not being used effectively
Observation data is the fruit of the BBS program; it must be harvested and effectively used. Yet, shortcomings in data analysis, publication and utilization are the Achilles heel of many BBS programs. This stems primarily from three basic reasons. First, typically the analysis of observation data is restricted to a select group of “trained” personnel. Second, observation data is not always available for use by line supervisors and employees. Third, conclusions from observation data and development of improvement plans are often not left to the people in the best position to affect immediate change, again the first line supervisor and the employees he/she works with. Each of these instances leaves supervisors and employees feeling left of the important decisions
they must own if true improvement is to take place.
SOLUTION
Pertinent observation data must be available and systematically reviewed with affected personnel. Data analysis and improvement planning should be conducted by those with the strongest vested interest and that is the supervisor and his/her employees. Subject Matter Experts should assist upon request. Improvement planning effectiveness must be routinely measured by affected management. Our TIPPS 3 database was specifically designed to facilitate the easy usage of BBS data. It is a web-based, all-in-one, reporting, tracking and planning system that amplifies employee involvement and execution. TIPPS 3 encompasses all the necessary safety & management tools to operate at peak performance. With its easy to use technology and engaging interface, TIPPS 3 saves time, money and yields best-in-class results that you can see in real-time.
Follow The SRI Group on LinkedIn for more
Follow Here