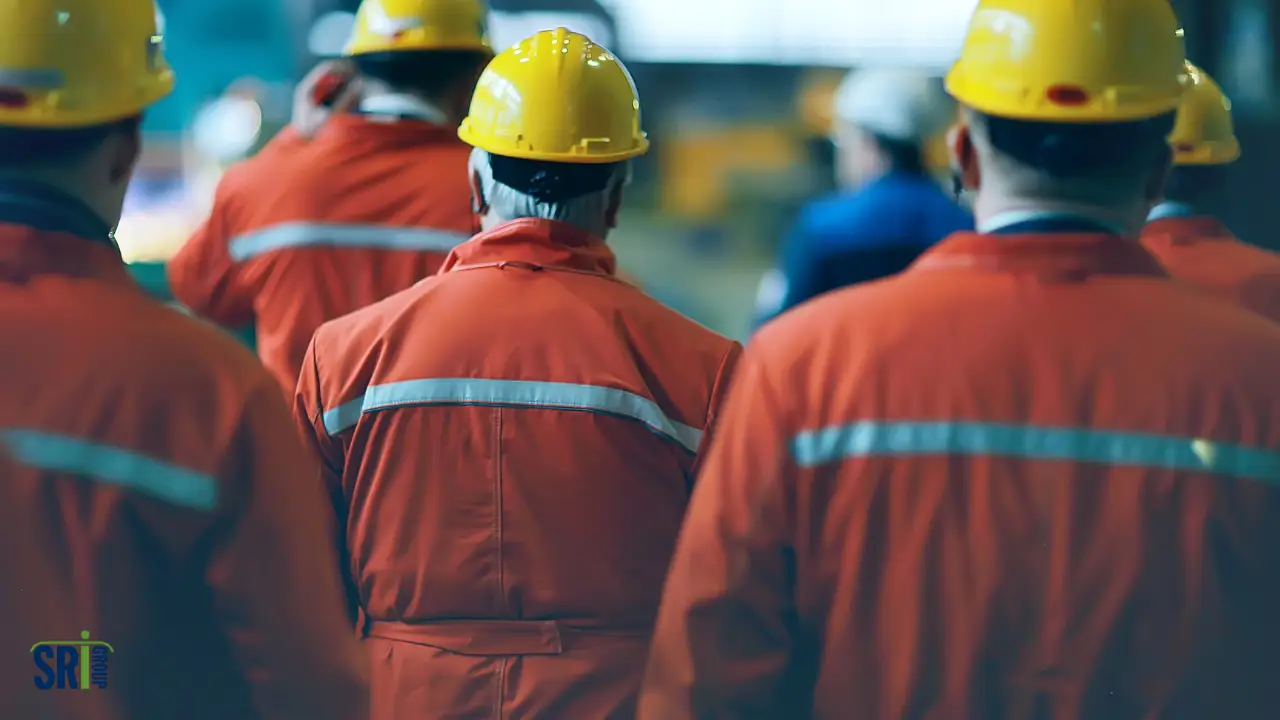
Why Regression Occurs in Safety – How to Fix it
Like top athletes, even high-performing companies can hit a slump. Things seem smooth, then suddenly, we wonder, “What’s happening?” At The SRI Group™, we’ve worked with hundreds of global clients. Over 30% of them were top performers, but faced stagnation or decline. In this article, we’ll explore common reasons for safety performance regression and strategies to regain desired results.
There are a number of factors which can lead to increased incidents or loss. In our work with top quartile performers we have identified five factors which often contribute to this safety performance regression:
• Forgetting the basics
• Poorly managed change
• Program overload
• Over-reliance on credentials and procedures
• Managing result versus processes
Stop HSE Regression
The Structured Safety Process (SSP) is the proven best practice to halt safety regression in its tracks.
Steps to Stop Regression
Issue #1 Forgetting Safety Basics
An EHS Manager from a large company once shared his thoughts on the cause of their recent increase in incidents: “We forgot the basics.” In their pursuit of better results, the company failed to transfer their “DNA” to a new generation of employees who hadn’t experienced the journey firsthand. These employees were trained on current requirements, but the foundational groundwork that led to initial excellence was overlooked.
Theses basics serve as the foundation for every successful safety system.
• Committed, involved leadership
• Developed roles and responsibilities
• Sequential meetings
• Safe work environment
• Clear, simple, concise procedures
• Committed to compliance
• Effective training
• Highly involved employees
• Knowledgeable and competent supervision
• An adult approach to accountability
When any of these 10 building blocks of safety excellence are not continually reinforced and renewed, then safety performance regression is inevitable. No matter how good you are, ask yourself, “are we taking care of the basics? Do we transmit the who / when / how / and most importantly why to each new employee?”
Solution #1
The solution is straightforward: emphasize the basics. Annually refresh employees’ knowledge of the fundamentals of your safety management system. Don’t assume that once something is learned, it’s retained forever. Ensure new hires understand their roles, responsibilities, and how to execute them. Highlight the value and importance of these activities for individuals, coworkers, and the organization. Regularly evaluate knowledge and execution of the basics, and never assume the organization has outgrown them.
Issue #2 Poorly Managed Change
Change is inevitable and, if managed well, can lead to exciting opportunities. However, poor management can have devastating effects. We’ll discuss two change-related challenges faced by our new clients.
First, rapid growth, mergers, or downsizing can result in inadequate planning and poor personnel change management. Executive leadership often focuses on cost, cash flow, and delivery, but may overlook safety, process safety, and risk. While corporate EHS staff might develop plans to mitigate negative effects, lack of support and prioritization from leadership can lead to increased incidents and losses.
When significant company changes occur, organizations are restructured, affecting responsibility for critical process activities. We often see a “wait and see” approach or delayed analysis of change effects, leading to poor execution of critical systems and confusion about responsibilities.
Second, modifying existing processes to fit a new organizational structure can create issues. While robust processes can sustain some change, significant alterations causing confusion about ownership and accountability can result in execution problems.
Solution #2
To avoid negative effects of change when there is a significant shift in the size or ownership of an organization, EHS issues must be fully integrated into the planning process. Operational leadership and business leadership must both understand the potential effects of these changes on safety performance and ensure plans are developed to eliminate or mitigate potential problems. Plans dealing with how to manage the change must be detailed and thoroughly thought through down to the operational level. Existing processes must be examined for potential changes in ownership or ability to execute requirements and these changes must be planned for. New assignments must be formally conveyed and appropriate training must be given to all those effected by the change.
Issue #3 Program Overload
Many companies fall into the trap of thinking “more is better,” but this isn’t always true.
In pursuit of reducing incidents and errors, some organizations add numerous prevention activities, believing it will improve performance. However, SRI has found that the quality of prevention activities often outweighs the benefits of volume. When efforts to meet requirements seem unnecessary, and the results aren’t utilized, employees may start doubting their importance. Moreover, if activities are mandated too frequently, employees will have to prioritize some over others, potentially neglecting important tasks.
Solution #3
When risks are heightened more may be better; more coaching, more planning, more discussion, but don’t assume that an uptick in incidents can be cured by more. Focus on the quality of the prevention activities currently being completed. Ensure these activities are being complete in a purposeful manner with attention to intent and value. Increase coaching by managers and supervision, and always reinforce good work when found. EHS professionals and leadership from the line organization must be aware of the requirements being place on personnel from every process and must work diligently to ensure work-loads are manageable. Synergize activities when possible, and if not possible, then prioritize.
Issue #4 Over-reliance on Credentials
Achieving VPP Star Status or OHSAS 18001 is commendable. For top performers, these recognitions validate their excellent systems and programs. However, when companies treat them as end goals, they may lose enthusiasm or rest on their laurels. We’ve seen clients focus on achieving recognition without ensuring lasting system changes, leaving them with unsuitable structures.
Another pitfall is the belief that all EHS programming can be captured in procedures. Work tasks have significant and minor variables, the latter posing little to no risk. Trying to capture all these details results in wasted time, unmanageable procedures, increased training costs, employee frustration, and stressed document control systems. Remember to keep procedures clear, simple, and concise. Clients sustaining excellence understand that they can’t account for every variable in each task.
Solution #4
Top-performing organizations recognize that achieving recognition or certification is just the beginning of their journey, and maintaining engagement and purpose requires specific strategies. These companies understand the need for diligence in executing safety systems and managing newly developed programs to maturity.
The key advantage for our best clients lies in their HES Management System, designed to serve their organization’s needs rather than just achieving a specific certification. As a result, their systems are robust, adaptable to various agency requirements, and can evolve to address new challenges while still meeting certification criteria.
Issue #5 Managing Results versus Processes
Organizations sometimes experience sudden spikes in injury rates after long periods of low incidents. The cause can often be attributed to an overemphasis on measuring results rather than processes. Performance evaluations, bonuses, and other incentives tied to statistics like Total Recordable Incident Rate can create pressure to “manage” injuries and discourage reporting.
Additionally, near-miss incidents may have occurred, signaling that safety processes aren’t functioning as intended. Over-focusing on results can lead to dismissing these incidents without proper examination and attention. At SRI, we emphasize the importance of measuring processes and addressing warning signs to maintain a safe environment.
Solution #5
Top-performing organizations focus on measuring processes and emphasize leading indicators. Their approach to performance evaluation and remuneration includes a mix of statistical performance, individual responsibilities, group goals, and evaluations of systems and activities for which the individual is accountable.
These organizations excel at reporting and addressing errors. They investigate incidents based on potential severity, not just the damage or harm caused. While these aren’t the only challenges faced by best-in-class organizations, nor the only potential solutions, they highlight some common problems and responses encountered in the pursuit of an incident-free work environment.